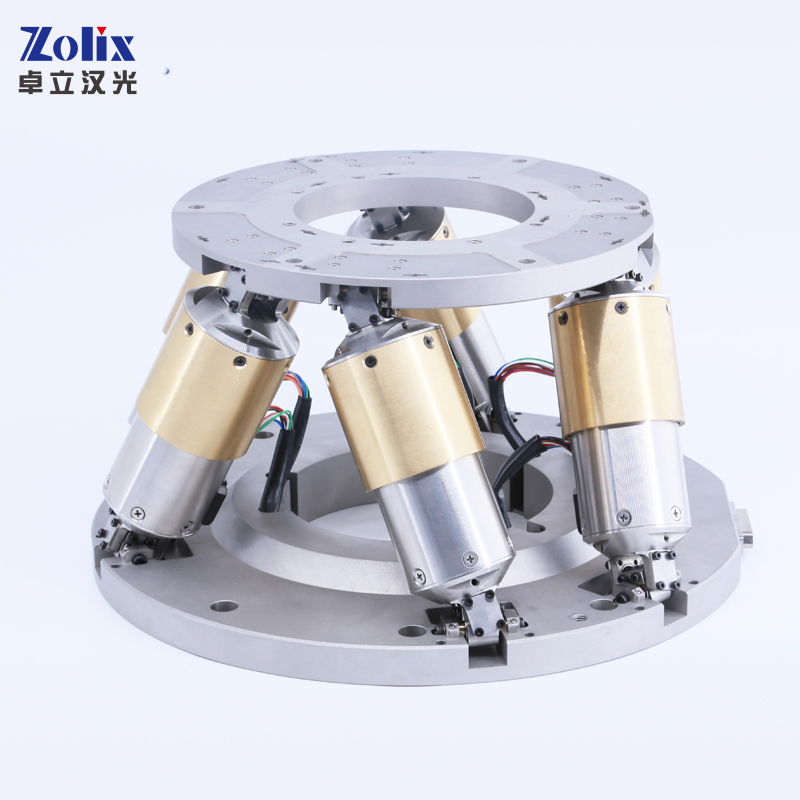
HXP High Precision Hexapod
HXP high precison hexapod is is mainly used for high-precision six-degree-of-freedom adjustment, and is particularly suitable for spacial precision alignment, micro-device processing and assembly, optical communication device core adjustment, wafer inspection and other occasions.
Features:
Show Filters:
Decription:
HXP high precison hexapod is is mainly used for high-precision six-degree-of-freedom adjustment, and is particularly suitable for spacial precision alignment, micro-device processing and assembly, optical communication device core adjustment, wafer inspection and other occasions. Structurally, the main body adopts six push rods + double Hook joint structure, which has the characteristics of strong rigidity, high repeatability, and can be installed in any position. The push rod can be selected with an absolute encoder or an incremental encoder. The push rod motor with an absolute encoder has the ability to maintain position information after power failure, and does not need to be reset after restart. The motor drive system uses the standard industrial bus EtherCAT for communication, which has high reliability and high communication efficiency, and is compatible with mainstream motion control systems on the market. The control system and software support various Euler angle space transformation formats, support robot operation space coordinate system management (including the setting and conversion of the world coordinate system, workpiece coordinate system (64 groups), robot installation coordinate system, robot drive coordinate system, and robot tool coordinate system (64 groups)), support load simulation, have robot space calibration function, support 3D posture simulation, teaching program and other functions. Provide secondary development package, which can be integrated into system equipment according to actual application.
Naming rules:
Main Features:
The control system and software support various Euler angle space transformation formats, support robot operation space coordinate system management (including the setting and conversion of the world coordinate system, workpiece coordinate system (64 groups), robot installation coordinate system, robot drive coordinate system, and robot tool coordinate system (64 groups)), support load simulation, have robot space calibration function, support 3D posture simulation, teaching program and other functions. Provide secondary development package, which can be integrated into system equipment according to actual application.
Model | HXP-824A | |
Travel X, Y(mm)* | ±34 | |
Travel Z(mm)* | ±15 | |
Travel θX, θY(°)* | ±11 | |
Travel θZ(°)* | ±25 | |
Push rod resolution(µm) | 0.25 | |
Min incremental motion X, Y, Z(µm)** | 1 | |
Min incremental motion θX, θY, θZ °** | 0.001 | |
Backlash X, Y(µm)** | 3 | |
Backlash Z(µm)** | 1 | |
BacklashθX, θY(”)** | 10 | |
Backlash θZ(”)** | 15 | |
Uni-repeatability X、Y(µm)** | ±0.5 | |
Uni-repeatability Z(µm)** | ±0.3 | |
Uni-repeatability θX, θY(”)** | ±2 | |
Uni-repeatability θZ(”)** | ±2.5 | |
Max speed of push rod(mm/s ) | 80 | |
Standard speed of push rod(mm/s ) | 40 | |
Horizontal load(Kg) | 20 | |
Load in any direction(Kg) | 2.5 | |
Motor type | Step-servo motor | |
Working temperature(℃) | +10 ~ +40 | |
Body material | SUS/Aluminium alloy | |
Weight(Kg) | 7 | |
Cable length(m) | 2 |